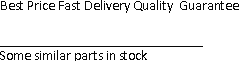
MAX11800ETC+T ,Low-Power, Ultra-Small Resistive Touch-Screen Controllers with I²C/SPI InterfaceFeatures Available in the MAX11800/MAX11801 Only . . . . . . . . . . . . . . . . . . . . . . . . . ..
MAX1182ECM+D ,Dual 10-Bit, 65Msps, +3V, Low-Power ADC with Internal Reference and Parallel OutputsApplicationsV 6 31 OGNDDDMAX1182GND 7 30 D0BHigh Resolution ImagingINB- 8 29 D1BI/Q Channel Digitiz ..
MAX1182ECM+TD ,Dual 10-Bit, 65Msps, +3V, Low-Power ADC with Internal Reference and Parallel OutputsELECTRICAL CHARACTERISTICS(V = +3V, OV = +2.5V; 0.1µF and 1.0µF capacitors from REFP, REFN, and COM ..
MAX1183ECM+D ,Dual 10-Bit, 40Msps, 3V, Low-Power ADC with Internal Reference and Parallel OutputsELECTRICAL CHARACTERISTICS(V = 3V, OV = 2.5V, 0.1µF and 1.0µF capacitors from REFP, REFN, and COM t ..
MAX1183ECM-D ,Dual 10-Bit, 40Msps, 3V, Low-Power ADC with Internal Reference and Parallel OutputsApplicationsINA- 5 32 OVDDV 6 31 OGNDDDMAX1183High-Resolution ImagingGND 7 30 D0BINB- 8 29 D1BI/Q C ..
MAX1185ECM+TD ,Dual 10-Bit, 20Msps, +3V, Low-Power ADC with Internal Reference and Multiplexed Parallel OutputsApplicationsINB- 8 29 N.C.INB+ 9 28 N.C.High Resolution ImagingGND 10 27 N.C.I/Q Channel Digitizati ..
MAX3490ECSA ,3.3V-Powered / 15kV ESD-Protected / 12Mbps and Slew-Rate-Limited True RS-485/RS-422 Transceivers
MAX3490ECSA ,3.3V-Powered / 15kV ESD-Protected / 12Mbps and Slew-Rate-Limited True RS-485/RS-422 Transceivers
MAX3490ECSA+ ,3.3V Powered, ±15kV ESD-Protected, 12Mbps, Slew-Rate-Limited True RS-485/RS-422 Transceivers
MAX3490ECSA+T ,3.3V Powered, ±15kV ESD-Protected, 12Mbps, Slew-Rate-Limited True RS-485/RS-422 Transceivers
MAX3490EEPA+ ,3.3V Powered, ±15kV ESD-Protected, 12Mbps, Slew-Rate-Limited True RS-485/RS-422 Transceivers
MAX3490EESA ,3.3V-Powered / 15kV ESD-Protected / 12Mbps and Slew-Rate-Limited True RS-485/RS-422 Transceivers
MAX11800ETC+T
Low-Power, Ultra-Small Resistive Touch-Screen Controllers with I²C/SPI Interface
General DescriptionThe MAX11800–MAX11803 low-power touch-screen con-
trollers operate from a single supply of 1.70V to 3.6V, tar-
geting power-sensitive applications such as handheld
equipment. The devices contain a 12-bit SAR ADC and a
multiplexer to interface with a resistive touch-screen
panel. A digital serial interface provides communications.
The MAX11800–MAX11803 include digital preprocessing
of the touch-screen measurements, reducing bus loading
and application-processor resource requirements. The
included smart interrupt function generator greatly
reduces the frequency of interrupt servicing to the
devices. The MAX11800–MAX11803 enter low-power
modes automatically between conversions to save power,
making the devices ideal for portable applications.
The MAX11800/MAX11801 offer two modes of operation:
direct and autonomous. Direct mode allows the applica-
tion processor to control all touch-screen controller activ-
ity. Autonomous mode allows the MAX11800/MAX11801
to control touch-screen activity, thereby freeing the
application processor to perform other functions. In
autonomous mode, the devices periodically scan the
touch screen for touch events without requiring host-
processor intervention. This can be used to reduce sys-
tem power consumption. An on-chip FIFO is used during
autonomous mode to store results, increasing effective
data throughput and lower system power.
The MAX11800–MAX11803 support data-tagging,
which records the type of measurement performed; X,
Y, Z1, or Z2, and the type of touch event; initial touch,
continuing touch, or touch release.
The MAX11800/MAX11802 support the SPI™ serial bus.
The MAX11801/MAX11803 support the I2C serial bus.
The MAX11800–MAX11803 are available in 12-pin TQFN
and 12-pin WLP packages, and are specified over the
-40°C to +85°C (extended) and -40°C to +105°C (auto-
motive) temperature ranges.
Applications
Features4-Wire Touch-Screen InterfaceX/Y Coordinate and Touch Pressure MeasurementRatiometric Measurement12-Bit SAR ADCSingle 1.7V to 3.6V SupplyTwo Operating Modes—Direct and AutonomousData Tagging Provides Measurement and Touch
Event InformationData Filtering Provides Noise ReductionAperture Mode Provides Spatial FilteringDigital Processing Reduces Bus Activity and
Interrupt GenerationProgrammable Touch-Detect Pullup ResistorsAuto Power-Down Control for Low-Power
Operation25MHz SPI Interface (MAX11800/MAX11802)400kHz I2C Interface (MAX11801/MAX11803)1.6mm x 2.1mm, 12-Pin WLP and 4mm x 4mm,
12-Pin TQFNLow-Power Operation
343µW at VDD= 1.7V, 34.4ksps
888µW at VDD= 3.3V, 34.4kspsESD Protection
±4kV HBM
±8kV HBM (X+, X-, Y+, Y-)
±1kV CDM
±200V MM
MAX11800–MAX11803
Low-Power, Ultra-Small Resistive ouch-Screen Controllers with I2C/SPI Interface
Ordering Information19-4711; Rev 3; 10/10
EVALUATION KIT
AVAILABLE
PARTTEMP RANGEPIN-PACKAGE
MAX11800ETC+ -40°C to +85°C 12 TQFN-EP*
MAX11800GTC/V+ -40°C to +105°C 12 TQFN-EP*
MAX11800EWC+T -40°C to +85°C 12 WLP
MAX11801ETC+ -40°C to +85°C 12 TQFN-EP*
MAX11801GTC/V+ -40°C to +105°C 12 TQFN-EP*
MAX11801EWC+T -40°C to +85°C 12 WLP
MAX11802ETC+ -40°C to +85°C 12 TQFN-EP*
MAX11802EWC+T -40°C to +85°C 12 WLP
MAX11803ETC+ -40°C to +85°C 12 TQFN-EP*
MAX11803EWC+T -40°C to +85°C 12 WLP
Typical Operating Circuits and Pin Configurations appear
at end of data sheet.+Denotes a lead(Pb)-free/RoHS-compliant package.
/V denotes an automotive qualified part.
T = Tape and reel.
Mobile Communication
Devices
PDAs, GPS Receivers,
Personal Navigation
Devices, Media Players
Portable Instruments
POS Terminals
Handheld Games
Automotive Center
Consoles
SPI is a trademark of Motorola, Inc.
MAX11800–MAX11803
Low-Power, Ultra-Small Resistive Touch-Screen
Controllers with I2C/SPI Interface
TABLE OF CONTENTSAbsolute Maximum Ratings . . . . . . . . . . . . . . . . . . . . . . . . . . . . . . . . . . . . . . . . . . . . . . . . . . . . . . . . . . . . . . . . . . . . . .8
Electrical Characteristics . . . . . . . . . . . . . . . . . . . . . . . . . . . . . . . . . . . . . . . . . . . . . . . . . . . . . . . . . . . . . . . . . . . . . . . .8
I2C Timing Characteristics . . . . . . . . . . . . . . . . . . . . . . . . . . . . . . . . . . . . . . . . . . . . . . . . . . . . . . . . . . . . . . . . . . . . . . .9
SPI Timing Characteristics . . . . . . . . . . . . . . . . . . . . . . . . . . . . . . . . . . . . . . . . . . . . . . . . . . . . . . . . . . . . . . . . . . . . . .10
Typical Operating Characteristics . . . . . . . . . . . . . . . . . . . . . . . . . . . . . . . . . . . . . . . . . . . . . . . . . . . . . . . . . . . . . . . .12
Pin Description . . . . . . . . . . . . . . . . . . . . . . . . . . . . . . . . . . . . . . . . . . . . . . . . . . . . . . . . . . . . . . . . . . . . . . . . . . . . . . .14
Functional Diagrams . . . . . . . . . . . . . . . . . . . . . . . . . . . . . . . . . . . . . . . . . . . . . . . . . . . . . . . . . . . . . . . . . . . . . . . . . .15
Detailed Description . . . . . . . . . . . . . . . . . . . . . . . . . . . . . . . . . . . . . . . . . . . . . . . . . . . . . . . . . . . . . . . . . . . . . . . . . . .16
Position Measurements . . . . . . . . . . . . . . . . . . . . . . . . . . . . . . . . . . . . . . . . . . . . . . . . . . . . . . . . . . . . . . . . . . . . . .16
Pressure Measurements . . . . . . . . . . . . . . . . . . . . . . . . . . . . . . . . . . . . . . . . . . . . . . . . . . . . . . . . . . . . . . . . . . . . .19
Touch-Detect Modes and Options . . . . . . . . . . . . . . . . . . . . . . . . . . . . . . . . . . . . . . . . . . . . . . . . . . . . . . . . . . . . .20
PUR and PUF . . . . . . . . . . . . . . . . . . . . . . . . . . . . . . . . . . . . . . . . . . . . . . . . . . . . . . . . . . . . . . . . . . . . . . . . . .21
Idle Modes . . . . . . . . . . . . . . . . . . . . . . . . . . . . . . . . . . . . . . . . . . . . . . . . . . . . . . . . . . . . . . . . . . . . . . . . . . . .21
Features Available in the MAX11800–MAX11803 Averaging Modes . . . . . . . . . . . . . . . . . . . . . . . . . . . . . . . . . . .21
Combined Commands . . . . . . . . . . . . . . . . . . . . . . . . . . . . . . . . . . . . . . . . . . . . . . . . . . . . . . . . . . . . . . . . . . .23
Data Tagging . . . . . . . . . . . . . . . . . . . . . . . . . . . . . . . . . . . . . . . . . . . . . . . . . . . . . . . . . . . . . . . . . . . . . . . . . .23
Low-Power Modes . . . . . . . . . . . . . . . . . . . . . . . . . . . . . . . . . . . . . . . . . . . . . . . . . . . . . . . . . . . . . . . . . . . . . .23
Features Available in the MAX11800/MAX11801 Only . . . . . . . . . . . . . . . . . . . . . . . . . . . . . . . . . . . . . . . . . . . . . .24
Autonomous Mode . . . . . . . . . . . . . . . . . . . . . . . . . . . . . . . . . . . . . . . . . . . . . . . . . . . . . . . . . . . . . . . . . . . . . . . . .24
Aperture . . . . . . . . . . . . . . . . . . . . . . . . . . . . . . . . . . . . . . . . . . . . . . . . . . . . . . . . . . . . . . . . . . . . . . . . . . . . . . . . . .24
Panel Setup, Measurement, and Scan Commands . . . . . . . . . . . . . . . . . . . . . . . . . . . . . . . . . . . . . . . . . . . . .24
Direct Conversion Mode Operations . . . . . . . . . . . . . . . . . . . . . . . . . . . . . . . . . . . . . . . . . . . . . . . . . . . . . . . . . . . .24
Interrupt Modes . . . . . . . . . . . . . . . . . . . . . . . . . . . . . . . . . . . . . . . . . . . . . . . . . . . . . . . . . . . . . . . . . . . . . . . .24
Panel Setup Commands . . . . . . . . . . . . . . . . . . . . . . . . . . . . . . . . . . . . . . . . . . . . . . . . . . . . . . . . . . . . . . . . .27
Panel Measurement Commands . . . . . . . . . . . . . . . . . . . . . . . . . . . . . . . . . . . . . . . . . . . . . . . . . . . . . . . . . . .27
Combined Commands . . . . . . . . . . . . . . . . . . . . . . . . . . . . . . . . . . . . . . . . . . . . . . . . . . . . . . . . . . . . . . . . . . .28
Auxiliary Measurement Command . . . . . . . . . . . . . . . . . . . . . . . . . . . . . . . . . . . . . . . . . . . . . . . . . . . . . . . . . .28
Autonomous Conversion Mode . . . . . . . . . . . . . . . . . . . . . . . . . . . . . . . . . . . . . . . . . . . . . . . . . . . . . . . . . . . . . . . .31
Measurement Operations . . . . . . . . . . . . . . . . . . . . . . . . . . . . . . . . . . . . . . . . . . . . . . . . . . . . . . . . . . . . . . . .32
Combined Commands . . . . . . . . . . . . . . . . . . . . . . . . . . . . . . . . . . . . . . . . . . . . . . . . . . . . . . . . . . . . . . . . . . .32
Delayed Touch Detection During Mode Transitions . . . . . . . . . . . . . . . . . . . . . . . . . . . . . . . . . . . . . . . . . . . . .33
FIFO Memory . . . . . . . . . . . . . . . . . . . . . . . . . . . . . . . . . . . . . . . . . . . . . . . . . . . . . . . . . . . . . . . . . . . . . . . . . .33
Clearing FIFO . . . . . . . . . . . . . . . . . . . . . . . . . . . . . . . . . . . . . . . . . . . . . . . . . . . . . . . . . . . . . . . . . . . . . . . . . .33
FIFO Data Block Readback Structure . . . . . . . . . . . . . . . . . . . . . . . . . . . . . . . . . . . . . . . . . . . . . . . . . . . . . . .33
FIFO Data Word Structure . . . . . . . . . . . . . . . . . . . . . . . . . . . . . . . . . . . . . . . . . . . . . . . . . . . . . . . . . . . . . . . .34
Block Readback Operations . . . . . . . . . . . . . . . . . . . . . . . . . . . . . . . . . . . . . . . . . . . . . . . . . . . . . . . . . . . . . . .34
Clearing Interrupt . . . . . . . . . . . . . . . . . . . . . . . . . . . . . . . . . . . . . . . . . . . . . . . . . . . . . . . . . . . . . . . . . . . . . . .34
Aperture Modes and Options . . . . . . . . . . . . . . . . . . . . . . . . . . . . . . . . . . . . . . . . . . . . . . . . . . . . . . . . . . . . . .34
Aperture Range Requirements . . . . . . . . . . . . . . . . . . . . . . . . . . . . . . . . . . . . . . . . . . . . . . . . . . . . . . . . . . . . .34
FIFO Aperture Criteria . . . . . . . . . . . . . . . . . . . . . . . . . . . . . . . . . . . . . . . . . . . . . . . . . . . . . . . . . . . . . . . . . . . .35
Applications Information . . . . . . . . . . . . . . . . . . . . . . . . . . . . . . . . . . . . . . . . . . . . . . . . . . . . . . . . . . . . . . . . . . . . . . .35
Using Aperture Mode . . . . . . . . . . . . . . . . . . . . . . . . . . . . . . . . . . . . . . . . . . . . . . . . . . . . . . . . . . . . . . . . . . . . . . .35
MAX11800–MAX11803
Low-Power, Ultra-Small Resistive Touch-Screen
Controllers with I2C/SPI Interface
TABLE OF CONTENTS (continued)Examples of Using Aperture Mode . . . . . . . . . . . . . . . . . . . . . . . . . . . . . . . . . . . . . . . . . . . . . . . . . . . . . . . . . . . . .36
SPI Communication Sequence (MAX11800/MAX11802) . . . . . . . . . . . . . . . . . . . . . . . . . . . . . . . . . . . . . . . . . . . .38
SPI Configuration Register Write (MAX11800/MAX11802) . . . . . . . . . . . . . . . . . . . . . . . . . . . . . . . . . . . . . . . .38
SPI Configuration or Result Register Read (MAX11800/MAX11802) . . . . . . . . . . . . . . . . . . . . . . . . . . . . . . . .39
SPI Conversion Command (MAX11800/MAX11802) . . . . . . . . . . . . . . . . . . . . . . . . . . . . . . . . . . . . . . . . . . . .40
I2C-Supported Sequence (MAX11801/MAX11803) . . . . . . . . . . . . . . . . . . . . . . . . . . . . . . . . . . . . . . . . . . . . . . . .40
Bit Transfer . . . . . . . . . . . . . . . . . . . . . . . . . . . . . . . . . . . . . . . . . . . . . . . . . . . . . . . . . . . . . . . . . . . . . . . . . . . . . . .40
START and STOP Conditions . . . . . . . . . . . . . . . . . . . . . . . . . . . . . . . . . . . . . . . . . . . . . . . . . . . . . . . . . . . . . . . . .40
Early STOP Conditions . . . . . . . . . . . . . . . . . . . . . . . . . . . . . . . . . . . . . . . . . . . . . . . . . . . . . . . . . . . . . . . . . . . . . .41
Slave Address . . . . . . . . . . . . . . . . . . . . . . . . . . . . . . . . . . . . . . . . . . . . . . . . . . . . . . . . . . . . . . . . . . . . . . . . . . . . .41
I2C Register Address . . . . . . . . . . . . . . . . . . . . . . . . . . . . . . . . . . . . . . . . . . . . . . . . . . . . . . . . . . . . . . . . . . . . . . .41
Acknowledge . . . . . . . . . . . . . . . . . . . . . . . . . . . . . . . . . . . . . . . . . . . . . . . . . . . . . . . . . . . . . . . . . . . . . . . . . . . . . .41
Write Data Format . . . . . . . . . . . . . . . . . . . . . . . . . . . . . . . . . . . . . . . . . . . . . . . . . . . . . . . . . . . . . . . . . . . . . . . . . .42
Read Data Format . . . . . . . . . . . . . . . . . . . . . . . . . . . . . . . . . . . . . . . . . . . . . . . . . . . . . . . . . . . . . . . . . . . . . . . . . .43
Streamlined I2C Read Operations . . . . . . . . . . . . . . . . . . . . . . . . . . . . . . . . . . . . . . . . . . . . . . . . . . . . . . . . . .44
I2C Conversion and Measurement Commands (MAX11801/MAX11803) . . . . . . . . . . . . . . . . . . . . . . . . . . . . . . . .45
Command and Register Map . . . . . . . . . . . . . . . . . . . . . . . . . . . . . . . . . . . . . . . . . . . . . . . . . . . . . . . . . . . . . . . . .45
User-Accessible Registers . . . . . . . . . . . . . . . . . . . . . . . . . . . . . . . . . . . . . . . . . . . . . . . . . . . . . . . . . . . . . . . .45
Status and Configuration Registers . . . . . . . . . . . . . . . . . . . . . . . . . . . . . . . . . . . . . . . . . . . . . . . . . . . . . . . . .46
Data Readback Commands . . . . . . . . . . . . . . . . . . . . . . . . . . . . . . . . . . . . . . . . . . . . . . . . . . . . . . . . . . . . . . . . . .46
Autonomous Conversion Mode . . . . . . . . . . . . . . . . . . . . . . . . . . . . . . . . . . . . . . . . . . . . . . . . . . . . . . . . . . . .46
Direct Conversion Mode . . . . . . . . . . . . . . . . . . . . . . . . . . . . . . . . . . . . . . . . . . . . . . . . . . . . . . . . . . . . . . . . . .46
Panel Setup and Measurement Commands . . . . . . . . . . . . . . . . . . . . . . . . . . . . . . . . . . . . . . . . . . . . . . . . . . . . . .48
User Configuration Registers . . . . . . . . . . . . . . . . . . . . . . . . . . . . . . . . . . . . . . . . . . . . . . . . . . . . . . . . . . . . . . . . . . . .49
General Status Register (0x00) (Read Only) . . . . . . . . . . . . . . . . . . . . . . . . . . . . . . . . . . . . . . . . . . . . . . . . . . . . . .49
General Configuration Register (0x01) . . . . . . . . . . . . . . . . . . . . . . . . . . . . . . . . . . . . . . . . . . . . . . . . . . . . . . . . . .50
Measurement Resolution Configuration Register (0x02) . . . . . . . . . . . . . . . . . . . . . . . . . . . . . . . . . . . . . . . . . . . . .50
Measurement Averaging Configuration Register (0x03) . . . . . . . . . . . . . . . . . . . . . . . . . . . . . . . . . . . . . . . . . . . . .51
ADC Sampling Time Configuration Register (0x04) . . . . . . . . . . . . . . . . . . . . . . . . . . . . . . . . . . . . . . . . . . . . . . . .51
Panel Setup Timing Configuration Register (0x05) . . . . . . . . . . . . . . . . . . . . . . . . . . . . . . . . . . . . . . . . . . . . . . . . .52
Delayed Conversion Configuration Register (0x06) . . . . . . . . . . . . . . . . . . . . . . . . . . . . . . . . . . . . . . . . . . . . . . . .52
Touch-Detect Pullup Timing Configuration Register (0x07) . . . . . . . . . . . . . . . . . . . . . . . . . . . . . . . . . . . . . . . . . .53
Autonomous Mode Timing Configuration Register (0x08) . . . . . . . . . . . . . . . . . . . . . . . . . . . . . . . . . . . . . . . . . . .54
Aperture Configuration Register (0x09) . . . . . . . . . . . . . . . . . . . . . . . . . . . . . . . . . . . . . . . . . . . . . . . . . . . . . . . . .54
Auxiliary Measurement Configuration Register (0x0A) . . . . . . . . . . . . . . . . . . . . . . . . . . . . . . . . . . . . . . . . . . . . . .55
Operating Mode Configuration Register (0x0B) . . . . . . . . . . . . . . . . . . . . . . . . . . . . . . . . . . . . . . . . . . . . . . . . . . .56
MAX11800/MAX11802 Typical Operating Circuit . . . . . . . . . . . . . . . . . . . . . . . . . . . . . . . . . . . . . . . . . . . . . . . . . . . .57
MAX11801/MAX11803 Typical Operating Circuit . . . . . . . . . . . . . . . . . . . . . . . . . . . . . . . . . . . . . . . . . . . . . . . . . . . .57
Pin Configurations . . . . . . . . . . . . . . . . . . . . . . . . . . . . . . . . . . . . . . . . . . . . . . . . . . . . . . . . . . . . . . . . . . . . . . . . . . . .58
Chip Information . . . . . . . . . . . . . . . . . . . . . . . . . . . . . . . . . . . . . . . . . . . . . . . . . . . . . . . . . . . . . . . . . . . . . . . . . . . . . .58
Package Information . . . . . . . . . . . . . . . . . . . . . . . . . . . . . . . . . . . . . . . . . . . . . . . . . . . . . . . . . . . . . . . . . . . . . . . . . .58
Revision History . . . . . . . . . . . . . . . . . . . . . . . . . . . . . . . . . . . . . . . . . . . . . . . . . . . . . . . . . . . . . . . . . . . . . . . . . . . . . .59
MAX11800–MAX11803
Low-Power, Ultra-Small Resistive Touch-Screen
Controllers with I2C/SPI InterfaceFigure 1. I2C Timing Diagram . . . . . . . . . . . . . . . . . . . . . . . . . . . . . . . . . . . . . . . . . . . . . . . . . . . . . . . . . . . . . . . . . . .10
Figure 2. SPI Timing Diagram . . . . . . . . . . . . . . . . . . . . . . . . . . . . . . . . . . . . . . . . . . . . . . . . . . . . . . . . . . . . . . . . . . .11
Figure 3a. MAX11800/MAX11801 Operation Modes . . . . . . . . . . . . . . . . . . . . . . . . . . . . . . . . . . . . . . . . . . . . . . . . . .17
Figure 3b. MAX11802/MAX11803 Operation Modes . . . . . . . . . . . . . . . . . . . . . . . . . . . . . . . . . . . . . . . . . . . . . . . . . .18
Figure 4. Position Measurements . . . . . . . . . . . . . . . . . . . . . . . . . . . . . . . . . . . . . . . . . . . . . . . . . . . . . . . . . . . . . . . . .19
Figure 5. Pressure Measurements . . . . . . . . . . . . . . . . . . . . . . . . . . . . . . . . . . . . . . . . . . . . . . . . . . . . . . . . . . . . . . . .19
Figure 6. Touch-Detection Circuitry . . . . . . . . . . . . . . . . . . . . . . . . . . . . . . . . . . . . . . . . . . . . . . . . . . . . . . . . . . . . . . .21
Figure 7. Touch-Detection Operations . . . . . . . . . . . . . . . . . . . . . . . . . . . . . . . . . . . . . . . . . . . . . . . . . . . . . . . . . . . . .22
Figure 8. State Machine Transitions (Direct Conversion Mode)—MAX11800–MAX11803 . . . . . . . . . . . . . . . . . . . . .25
Figure 9. Continuous Interrupt Mode (Direct Conversion Mode) . . . . . . . . . . . . . . . . . . . . . . . . . . . . . . . . . . . . . . . . .26
Figure 10. Edge Interrupt Mode (Direct Conversion Mode)—MAX11800–MAX11803 . . . . . . . . . . . . . . . . . . . . . . . .27
Figure 11. Command and Measurement Flow (DCM) . . . . . . . . . . . . . . . . . . . . . . . . . . . . . . . . . . . . . . . . . . . . . . . . .28
Figure 12. Panel Setup and Measurement Commands—MAX11800–MAX11803 . . . . . . . . . . . . . . . . . . . . . . . . . . .29
Figure 13. Combined Commands—MAX11800–MAX11803 . . . . . . . . . . . . . . . . . . . . . . . . . . . . . . . . . . . . . . . . . . . .30
Figure 14. State Machine Transitions––Autonomous Conversion Mode—MAX11800/MAX11801 . . . . . . . . . . . . . . .31
Figure 15. Clear-on-Read Interrupt Operation—MAX11800/MAX11801 . . . . . . . . . . . . . . . . . . . . . . . . . . . . . . . . . . .32
Figure 16. Aperture Usage Example Waveforms—MAX11800/MAX11801 . . . . . . . . . . . . . . . . . . . . . . . . . . . . . . . . .36
Figure 17. SPI Single Configuration Register Write Sequence—MAX11800/MAX11802 . . . . . . . . . . . . . . . . . . . . . .38
Figure 18. SPI Multiple Configuration Register Write Sequence—MAX11800/MAX11802 . . . . . . . . . . . . . . . . . . . . .38
Figure 19. SPI Single-Byte Register Read Sequence—MAX11800/MAX11802 . . . . . . . . . . . . . . . . . . . . . . . . . . . . .39
Figure 20. SPI Multiple-Byte Register Read Sequence—MAX11800/MAX11802 . . . . . . . . . . . . . . . . . . . . . . . . . . . .40
Figure 21. SPI Conversion Command—MAX11800/MAX11802 . . . . . . . . . . . . . . . . . . . . . . . . . . . . . . . . . . . . . . . . .40
Figure 22. 2-Wire Interface Timing Diagram . . . . . . . . . . . . . . . . . . . . . . . . . . . . . . . . . . . . . . . . . . . . . . . . . . . . . . . .41
Figure 23. START, STOP, and Repeated START Conditions . . . . . . . . . . . . . . . . . . . . . . . . . . . . . . . . . . . . . . . . . . . .41
Figure 24. Acknowledge . . . . . . . . . . . . . . . . . . . . . . . . . . . . . . . . . . . . . . . . . . . . . . . . . . . . . . . . . . . . . . . . . . . . . . .41
Figure 25. I2C Single Write Sequence . . . . . . . . . . . . . . . . . . . . . . . . . . . . . . . . . . . . . . . . . . . . . . . . . . . . . . . . . . . . .42
Figure 26. I2C Multiple Write Sequence . . . . . . . . . . . . . . . . . . . . . . . . . . . . . . . . . . . . . . . . . . . . . . . . . . . . . . . . . . . .42
Figure 27. Basic Single Read Sequence . . . . . . . . . . . . . . . . . . . . . . . . . . . . . . . . . . . . . . . . . . . . . . . . . . . . . . . . . . .43
Figure 28. I2C Multiple Read Sequence . . . . . . . . . . . . . . . . . . . . . . . . . . . . . . . . . . . . . . . . . . . . . . . . . . . . . . . . . . .43
Figure 29. I2C Streamlined Read Sequence . . . . . . . . . . . . . . . . . . . . . . . . . . . . . . . . . . . . . . . . . . . . . . . . . . . . . . . .44
Figure 30. I2C Conversion and Measurement Commands . . . . . . . . . . . . . . . . . . . . . . . . . . . . . . . . . . . . . . . . . . . . .45
LIST OF FIGURES
MAX11800–MAX11803
Low-Power, Ultra-Small Resistive Touch-Screen
Controllers with I2C/SPI Interface
LIST OF TABLESTable 1. Terminology . . . . . . . . . . . . . . . . . . . . . . . . . . . . . . . . . . . . . . . . . . . . . . . . . . . . . . . . . . . . . . . . . . . . . . . . . . .6
Table 2. Operating Modes, Conditions, and Options . . . . . . . . . . . . . . . . . . . . . . . . . . . . . . . . . . . . . . . . . . . . . . . . .19
Table 3. Summary of Physical Panel Settings for Supported Measurement Types . . . . . . . . . . . . . . . . . . . . . . . . . . .20
Table 4. Median Averaging Operations . . . . . . . . . . . . . . . . . . . . . . . . . . . . . . . . . . . . . . . . . . . . . . . . . . . . . . . . . . . .23
Table 5. Data Word Structure (All Direct Conversion Modes) . . . . . . . . . . . . . . . . . . . . . . . . . . . . . . . . . . . . . . . . . . .23
Table 6. Measurement and Event Tags (Continuous Interrupt Mode) . . . . . . . . . . . . . . . . . . . . . . . . . . . . . . . . . . . . .25
Table 7. Measurement and Event Tags (Edge Interrupt Mode) . . . . . . . . . . . . . . . . . . . . . . . . . . . . . . . . . . . . . . . . .26
Table 8. Panel Setup Command Summary . . . . . . . . . . . . . . . . . . . . . . . . . . . . . . . . . . . . . . . . . . . . . . . . . . . . . . . . .27
Table 9. Panel Measurement Command Summary . . . . . . . . . . . . . . . . . . . . . . . . . . . . . . . . . . . . . . . . . . . . . . . . . . .28
Table 10. FIFO Data Block Structure . . . . . . . . . . . . . . . . . . . . . . . . . . . . . . . . . . . . . . . . . . . . . . . . . . . . . . . . . . . . . .33
Table 11. FIFO Data Word Structure . . . . . . . . . . . . . . . . . . . . . . . . . . . . . . . . . . . . . . . . . . . . . . . . . . . . . . . . . . . . . .34
Table 12. FIFO Data Measurement Tags . . . . . . . . . . . . . . . . . . . . . . . . . . . . . . . . . . . . . . . . . . . . . . . . . . . . . . . . . . .34
Table 13. FIFO Event Tags . . . . . . . . . . . . . . . . . . . . . . . . . . . . . . . . . . . . . . . . . . . . . . . . . . . . . . . . . . . . . . . . . . . . . .34
Table 14. Readback and FIFO Contents with Aperture Mode Enabled . . . . . . . . . . . . . . . . . . . . . . . . . . . . . . . . . . .37
Table 15. Readback and FIFO Contents with Aperture Mode Disabled . . . . . . . . . . . . . . . . . . . . . . . . . . . . . . . . . . .37
Table 16. SPI Command and Data Format: 8 Bits . . . . . . . . . . . . . . . . . . . . . . . . . . . . . . . . . . . . . . . . . . . . . . . . . . . .46
Table 17. I2C Command and Data Format: 8 Bits Plus ACK . . . . . . . . . . . . . . . . . . . . . . . . . . . . . . . . . . . . . . . . . . . .46
Table 18. Status and Configuration Registers . . . . . . . . . . . . . . . . . . . . . . . . . . . . . . . . . . . . . . . . . . . . . . . . . . . . . .47
Table 19. Data Readback Command Summary . . . . . . . . . . . . . . . . . . . . . . . . . . . . . . . . . . . . . . . . . . . . . . . . . . . . .47
Table 20. Conversion Command Summary . . . . . . . . . . . . . . . . . . . . . . . . . . . . . . . . . . . . . . . . . . . . . . . . . . . . . . . . .48
Table 21. Measurement Commands . . . . . . . . . . . . . . . . . . . . . . . . . . . . . . . . . . . . . . . . . . . . . . . . . . . . . . . . . . . . . .49
MAX11800–MAX11803
Low-Power, Ultra-Small Resistive Touch-Screen
Controllers with I2C/SPI Interface
TERMDEFINITION
Panel,
Touch Screen,
Touch Panel
Resistive Touch Sensor: Panel, or touch screen, or touch panel are used interchangeably to denote the resistive touch sensor.
TSCTouch-Screen Controller: Devices attached to a touch screen that provide the interface between an application processor (AP) and touch screen.
X Position Positive I/O: Analog I/O from resistive touch screen. See Figure 4 for configuration and measurement details.
X Position Negative I/O: Analog I/O from resistive touch screen. See Figure 4 for configuration and measurement details.
Y Position Positive I/O: Analog I/O from resistive touch screen. See Figure 4 for configuration and measurement details.
Y Position Negative I/O: Analog I/O from resistive touch screen. See Figure 4 for configuration and measurement details.
RTOUCHTouch Resistance:Represents the resistance between the X and Y planes of a resistive touch screen during a
touch event.
Z1 Measurement: A resistive touch-screen measurement to determine the resistance between the two planes within the panel sensor during a touch event (RTOUCH). See Figure 5 for configuration and measurement details.
Z2 Measurement: A resistive touch-screen measurement to determine the resistance between the two planes within the panel sensor during a touch event (RTOUCH). See Figure 5 for configuration and measurement details.
AUXAuxiliary Input: Analog input to the MAX11800–MAX11803 that can be used to monitor external conditions such as battery voltage or temperature.
ADCAnalog-to-Digital Converter: Circuit used to transform analog information into a form suitable for digital operations. Application Processor: An external microcontroller or microprocessor that interfaces to and controls the general operation of the MAX11800–MAX11803.
AVGAveraging Mode: The ability to average consecutive measurement results to reduce noise from switch bounce, power-supply ripple, and incomplete settling.
MAFMedian Averaging Filter: The MAF first removes the minimum and maximum samples before taking the average of the remaining sample set.
SAFStraight Averaging Filter: The SAF takes the average of an entire sample set.
TDMTouch-Detect Mode: An untimed mode that monitors the panel for a touch using a user-selectable panel pullup resistor of either 50k or 100k.
DCM
Direct Conversion Mode: A mode of operation in which the AP requests individual panel setup and conversion operations or automated combinations of measurements (X and Y, X and Y and Z1, or X and Y and
Z1 and Z2). The AP maintains control over the initiation of panel setup, measurements, and the sampling
ACM
Autonomous Conversion Mode: A mode of operation in which the MAX11800/MAX11801 idle in TDM until a touch event occurs. After a touch is detected, the MAX11800/MAX11801 begin an automated sequence of
measurements determined by the user configuration registers.
PSU
Panel Setup Command: User-programmable modes for the purpose of allowing the panel sufficient time to settle, prior to the start of measurements. PSU commands configure the on-chip multiplexer in preparation to
perform either X, Y, Z1, or Z2 measurements. Durations can either be specified and managed by the
MAX11800–MAX11803 (in ACM and DCM) or managed by the AP (in DCM).
PMCPanel Measurement Command: Individual measurements of X or Y position and Z1 or Z2 pressure measurements.
CMCCombined Measurement Command: Combinations of PMCs (X and Y, X and Y and Z1, or X and Y and Z1 and Z2) offered by the MAX11800–MAX11803 and executed in series to reduce AP bus and interrupt activity.
Table 1. Terminology
MAX11800–MAX11803
Low-Power, Ultra-Small Resistive Touch-Screen
Controllers with I2C/SPI Interface
TERMDEFINITION
FIFO
First-In First-Out Memory: The MAX11800–MAX11803 contain a 1024-bit FIFO that is used to store conversionresults when operating in autonomous conversion mode. FIFO depth indicates the number of words (16-bit
quantity) in the FIFO.
ScanScan: Generally, a single sequence of operations performed in DCM or ACM. The operations could include apanel setup operation, followed by a panel measurement operation, or a combined measurement operation.
Scan BlockScan Block: Generally, a sequence of multiple operations performed in DCM or ACM. The operations couldinclude panel-setup operations, panel-measurement operations, or combined measurement operations.
Timed Scan
Timed Scan: A scan or scan block operation that uses the on-chip oscillator and timer. The timer is controlledthrough the configuration registers and represents an array of fixed (time) quantities that are user selectable
(MAX11800/MAX11801).
Untimed ScanUntimed Scan: A scan or scan block operation that is controlled by the AP. This only applies to DCM.
TAGD a t a Ta g : Infor m ati on ap p end ed to the end of an AD C conver si on r esul t. Tag s i nd i cate the typ e of m easur em ent and
touch status associ ated w i th each p anel ob ser vati on. S ee the d efi ni ti ons for E TAG and M TAG ( al so i n Tab l e 1) .
ETAGEvent Tag: Data tags indicating the panel touch status observed during a measurement.
MTAGMeasurement Tag: Data tag indicating the type of measurement read back by the AP (either X, Y, Z1, or Z2).TIRQ
Touch Interrupt Request: Active-low interrupt, indicating that a touch is present (CINT) or has been initiated(EINT) in DCM, or that new data is available in the FIFO in ACM.
EINTEdge Interrupt Mode: Indicates, through TIRQ, that a touch has been initiated (EINT) in DCM. The duration thatTIRQ is low is user programmable.
CINTContinuous Interrupt Mode: Indicates, through TIRQ, that a touch is present (CINT) in DCM. TIRQ goes low toindicate the presence of a touch and stays low until the touch event ceases.
CORINTClear-on-Read Interrupt Mode: Used in ACM only. TIRQ goes low to indicate the presence of new FIFO data. Theinterrupt is cleared when the data is read by the AP (MAX11800/MAX11801).
APERAperture Mode: Available in ACM only. Reduces data writes to the FIFO by spatially filtering measurement data.
CONTo n t i n u o u s B i t : An op ti on i n D C M to r etur n the MAX11800–MAX11803 to a p anel setup ( w ai t) m od e ( P S U ) after a
conver si on, r ather than a r etur n to TD M ( r ecom m end ed onl y for ap p l i cati ons w i th ver y l ong p anel settl i ng ti m es and eq uest contr ol l i ng thei r ow n aver ag i ng ) . The conti nuous b i t r esi d es i n b i t 0 ( R0) of the P S U and P M C r eg i ster s.
LPM
Low-Power Mode: An idle mode used in DCM/EINT or ACM modes, when a touch is detected at the conclusion ofthe last measurement. This indicates a new measurement needs to be requested or scheduled (the touch-detect
pullup is not engaged to save power).
PURPullup Rough: A fast pullup mode, which uses the main X+ switch in parallel with the on-chip resistive pullup(50kΩ/100kΩ) to quickly slew the touch panel capacitances. RPUR ≤ 10Ω typical.
PUFPullup Fine: A slow (fine) pullup mode, which uses the on-chip resistive pullup to slew the touch-panelcapacitances to their final values (RPUF = 50kΩ or 100kΩ) typical and is required for all applications.
SAR ADC
Successive Approximation Register ADC: An analog-to-digital converter that converts a continuous analogwaveform into a discrete digital representation through a binary search through all possible quantization levels
before finally converging upon a digital output for each conversion.
2C
Inter-Integrated Circuit: A multimaster serial computer bus that is used to attach low-speed peripherals to othercomponents using two bidirectional open-drain lines, serial data (SDA) and serial clock (SCL), pulled up with
resistors.
SPISerial Peripheral Interface: A serial interface in which a master device supplies clock pulses to exchange dataserially with a slave over two data wires (master-slave and slave-master).
Table 1. Terminology (continued)
MAX11800–MAX11803
Low-Power, Ultra-Small Resistive Touch-Screen
Controllers with I2C/SPI Interface
ELECTRICAL CHARACTERISTICS(VDD= 1.7V to 3.6V, TA= -40°C to +85°C (MAX11800E–MAX11803E), TA= -40°C to +105°C (MAX11800G/MAX11801G), unless oth-
erwise noted. Typical values are at TA= +25°C and VDD = 3.3V, unless otherwise noted.)
Stresses beyond those listed under “Absolute Maximum Ratings” may cause permanent damage to the device. These are stress ratings only, and functional
operation of the device at these or any other conditions beyond those indicated in the operational sections of the specifications is not implied. Exposure to
absolute maximum rating conditions for extended periods may affect device reliability.
VDDto GND...........................................................-0.3V to +4.0V
X+, X-, Y+, Y-, AUX, TIRQto GND........................-0.3V to +4.0V
SCL, CLK, SDA, DIN, A0, CS, A1, DOUT to GND.-0.3V to +4.0V
Maximum Current into Any Pin.........................................±50mA
Continuous Power Dissipation (TA= +70°C)
12-Pin TQFN (derate 24.4mW/°C above +70°C)....1951.2mW
12-Pin WLP (derate 6.5mW/°C above +70°C)..........518.8mW
Operating Temperature Ranges
MAX1180_E_ _..................................................-40°C to +85°C
MAX1180_G_ _...............................................-40°C to +105°C
Storage Temperature Range.............................-65°C to +150°C
Junction Temperature......................................................+150°C
Lead Temperature (excluding WLP, soldering, 10s).......+300°C
Soldering Temperature (reflow).......................................+260°C
PARAMETERSYMBOLCONDITIONSMINTYPMAXUNITS
ADCADC Resolution No missing codes 10 11 Bits
Differential Nonlinearity DNL 12-bit resolution ±1.5 LSB
Integral Nonlinearity INL 12-bit resolution ±1.5 LSB
Offset Error ±2 LSB
Gain Error ±4 LSB
Throughput 105 ksps
TOUCH SENSORS (X+, X-, Y+, Y-, AUX)VDD = 1.7V 7 Switch On-Resistance VDD = 3.3V 5
Switch Driver Current 100ms pulse 50 mA
Input Voltage Range 0 VDD V
POWER SUPPLY (VDD)Supply Voltage VDD 1.7 3.6 V
1.7V 0.2 Power-down mode. All digital
inputs static. 3.6V 2
TDM. All digital inputs static.
Does not include panel
currents when touched.
3.6V 7
1.7V 9 Timed LPM. All digital inputs
static. Does not include panel
currents when touched. 3.3V 16
1.7V 216 AUX conversions at 34.4ksps
equivalent rate, SPI 3.3V 273 550
1.7V 202
Supply Current
AUX conversions at 34.4ksps
equivalent rate, I2C3.3V 269 550
μA
1.7V 367 AUX conversions at 34.4ksps
equivalent rate, SPI 3.3V 901
1.7V 343 Power Consumption AUX conversions at 34.4ksps 2
μW
ABSOLUTE MAXIMUM RATINGS
Note 1:All WLP devices are 100% production tested at TA= +25°C. Specifications over temperature limits are guaranteed by
design and characterization.
MAX11800–MAX11803
Low-Power, Ultra-Small Resistive Touch-Screen
Controllers with I2C/SPI Interface
PARAMETERSYMBOLCONDITIONSMINTYPMAXUNITS
DIGITAL INPUTS (SDA, DIN, SCL, CLK, A0, CS, A1)Input Logic-High Voltage VIH0.7 x
VDD V
Input Logic-Low Voltage VIL 0.3 x
VDDV
Input Leakage Current IIN VIN = 0V or VDD -1 +1 μA
Input Hysteresis VHYS 0.5 x
VDD V
Input Capacitance 6 pF
DIGITAL OUTPUTS (SDA, DOUT, TIRQ)DOUT, ISOURCE = 1mA 0.9 x
VDDOutput Logic-High VOH
TIRQ, CMOS configuration,
ISOURCE = 1mA
0.9 x
VDD
Output Logic-Low—TIRQ, DOUT VOL ISINK = 1mA 0.4 V
Output Logic-Low—SDA VOL ISINK = 3mA 0.4 V
TIRQ Pullup Resistor 125 k
ELECTRICAL CHARACTERISTICS (continued)(VDD= 1.7V to 3.6V, TA= -40°C to +85°C (MAX11800E–MAX11803E), TA= -40°C to +105°C (MAX11800G/MAX11801G), unless oth-
erwise noted. Typical values are at TA= +25°C and VDD = 3.3V, unless otherwise noted.)
2C TIMING CHARACTERISTICS(VDD= 1.7V to 3.6V, TA= -40°C to +85°C (MAX11801E and MAX11803E), TA= -40°C to +105°C (MAX11801G), unless otherwise
noted. Typical values are at TA= +25°C and VDD= 3.3V, unless otherwise noted. See Figure 1.)
PARAMETERSYMBOLCONDITIONSMINTYPMAXUNITSSerial-Clock FrequencyfSCL0400kHz
Bus Free TimetBUFBus free time between STOP and START
condition1.3μs
Hold Time for START ConditiontHD;STAAfter this period, the first clock pulse is
generated0.6μs
SCL Pulse-Width LowtLOW1.3μs
SCL Pulse-Width HightHIGH0.6μs
Setup Time for Repeated START
(Sr) ConditiontSU;STA0.6μs
Data Hold TimetHD;DAT0900ns
Data Setup TimetSU;DAT100ns
SDA and SCL Rise/Fall TimetR, tFReceiving20 +
CB/10300ns
SDA and SCL Fall TimetTFTransmitting20 +
CB/10250ns
Setup Time for STOP ConditiontSU;STO0.6μs
VDD = 1.7V to 2.7V10100Bus Capacitance AllowedCBVDD = 2.7V to 3.6V10400pF
Pulse Width of Suppressed SpiketSP50ns
MAX11800–MAX11803
Low-Power, Ultra-Small Resistive Touch-Screen
Controllers with I2C/SPI Interface
SPI TIMING CHARACTERISTICS(VDD= 1.7V to 3.6V, TA= -40°C to +85°C (MAX11800E and MAX11802E), TA= -40°C to +105°C (MAX11800G), unless otherwise
noted. Typical values are at TA= +25°C and VDD= 3.3V, unless otherwise noted. See Figure 2.)
PARAMETERSYMBOLCONDITIONSMINTYPMAXUNITSCLK FrequencyfCLK25MHz
CLK PeriodtCP40ns
CLK Pulse-Width HightCH18ns
CLK Pulse-Width LowtCL18ns
CS Low to 1st CLK Rise SetuptCSS018ns
CS Low After 0th CLK Rise HoldtCSH0To prevent a 0th CLK read from being taken
as a 1st read in a free-running application0ns
CS High to 17th CLK SetuptCSS1
To prevent a 17th CLK read from being
recognized by the device in a free-running
applicationns
CS High After 16th CLK Falling
Edge HoldtCSH10ns
CS Pulse-Width HightCSW18ns
DIN to CLK SetuptDS25ns
DIN Hold After CLKtDH0ns
DOUT Transition Valid After CLK
RisetDOTOutput transition time25ns
DOUT Remains Valid After CLK
RisetDOHOutput hold time3ns
DOUT Valid Before CLK RisetDO1tDO1 = tCP - tDOT10ns
CS Rise to DOUT DisabletDODCLOAD = 20pF40ns
CLK Rise to DOUT EnabletDOE
CLOAD = 20pF. Minimum = hold time with
regard to 8th CLK read. Maximum =
transition time with regard to 8th CLK read.
325ns
SDA
SCL
tHD;STA
tLOW
tHD;DAT
tSU;DAT
tHIGHtSU;STA
tHD;STA
tSP
tBUF
tSU;STOS
MAX11800–MAX11803
Low-Power, Ultra-Small Resistive Touch-Screen
Controllers with I2C/SPI Interface08916
XA6A5A4A3A2A1A0WD7D6D5D4D3D2D1D0DIN
CLK
tCSH0
tDS
tDH
tCL
tCH
tCP
tCSW
tCSS1
tSCH1
DOUTHIGH-Z
SPI WRITE OPERATION8916A6A5A4A3A2A1A0RXXXXXXXXDIN
CLK
tCSS0
tDS
tDH
tCL
tCH
tCPtDO0
DOUTHIGH-Z
SPI READ OPERATION
tDOE
tDO1
tDOHD6D5D4D3D2D1D0HIGH-Z
tCSS0
Figure 2. SPI Timing Diagram
MAX11800–MAX11803
Low-Power, Ultra-Small Resistive Touch-Screen
Controllers with I2C/SPI InterfaceAVERAGE SUPPLY CURRENT
vs. SAMPLING RATE
MAX11800 toc01
SAMPLING RATE (cps)
SUPPLY CURRENT (
AUTONOMOUS MODE
MAX11800
MAX11801
cps = COORDINATES
PER SECOND
DATA TAKEN WITH
RESISTIVE TOUCH
SENSOR
AVERAGE SUPPLY CURRENT
vs. SAMPLING RATE
MAX11800 toc02
SAMPLING RATE (cps)
SUPPLY CURRENT (
DIRECT CONTINUOUS
INTERRUPT MODE
cps = COORDINATES PER SECOND
AVERAGE SUPPLY CURRENT
vs. SAMPLING RATE
MAX11800 toc03
SAMPLING RATE (cps)
SUPPLY CURRENT (
DIRECT EDGE
INTERRUPT MODE
cps = COORDINATES PER SECOND
SUPPLY CURRENT IN POWER-DOWN
vs. TEMPERATURE
MAX11800 toc04
TEMPERATURE (NC)
POWER-DOWN SUPPLY CURRENT (3510-15
SWITCH RESISTANCE
vs. SUPPLY VOLTAGE
MAX11800 toc05
VDD (V)
1.63.6Y-
SWITCH RESISTANCE
vs. TEMPERATURE
MAX11800 toc06
TEMPERATURE (NC)3510-15
CHANGE IN ADC GAIN
vs. TEMPERATURE
MAX11800 toc07
TEMPERATURE (NC)
DELTA FROM +25
C (LSB)50-1020
CHANGE IN ADC OFFSET
vs. TEMPERATURE
MAX11800 toc08
TEMPERATURE (NC)
DELTA FROM +25
C (LSB)50-1020
Typical Operating Characteristics
(VDD= 1.8V at TA= -40°C to +85°C (TA= -40°C, TA= 0°C, TA= +25°C, and TA= +85°C), 12-bit mode, all measurements using
noncontinuous AUX input. SPI = 10MHz and I2C = 400kHz, unless otherwise noted. Resistive touch-screen panel (X+ to X- = 608Ω,
Y+ to Y- = 371Ω).)
MAX11800–MAX11803
Low-Power, Ultra-Small Resistive Touch-Screen
Controllers with I2C/SPI InterfaceAVERAGE SUPPLY CURRENT
vs. SAMPLING RATE
MAX11800 toc09
SAMPLING RATE (sps)
SUPPLY CURRENT (
DIRECT CONVERSION
MODE—AUXILIARY INPUT
sps = SAMPLES PER SECOND
AVERAGE SUPPLY CURRENT
vs. SAMPLING RATE
MAX11800 toc10
EQUIVALENT SAMPLING RATE (ksps)
SUPPLY CURRENT (16
AUXILIARY INPUT DATA
SAMPLED AT 1ksps AND
2ksps WITH EIGHT AND
16 SAMPLES
AVERAGING
ENABLED
ksps = KILO-SAMPLES PER SECOND
INTERNAL OSCILLATOR CLOCK
FREQUENCY vs. TEMPERATURE
MAX11800 toc11
TEMPERATURE (NC)
INTERNAL OSCILLATOR CLOCK FREQUENCY (MHz)3510-15
VDD = 3.6V
VDD = 1.8V
VDD = 3.0V
INTERNAL OSCILLATOR CLOCK
FREQUENCY vs. SUPPLY VOLTAGE
MAX11800 toc12
VDD (V)
INTERNAL OSCILLATOR CLOCK FREQUENCY (MHz)
POWER CONSUMPTION
vs. SAMPLE RATE
MAX11800 toc13
SAMPLE RATE (cps)
POWER CONSUMPTION (
DATA TAKEN WITH
RESISTIVE TOUCH SENSOR
AUTONOMOUS MODE*
*MAX11800/MAX11801
DIRECT CONTINUOUS MODE
DIRECT EDGE MODE
cps = COORDINATES
PER SECOND
Typical Operating Characteristics (continued)(VDD= 1.8V at TA= -40°C to +85°C (TA= -40°C, TA= 0°C, TA= +25°C, and TA= +85°C), 12-bit mode, all measurements using
noncontinuous AUX input. SPI = 10MHz and I2C = 400kHz, unless otherwise noted. Resistive touch-screen panel (X+ to X- = 608Ω,
Y+ to Y- = 371Ω).)
MAX11800–MAX11803
Low-Power, Ultra-Small Resistive Touch-Screen
Controllers with I2C/SPI Interface
Pin Description
PIN
MAX11800/MAX11802 MAX11801/MAX11803
TQFN-EPWLPTQFN-EPWLP
NAMEFUNCTION 1 A4 1 A4 X+ X+ Channel Input/Output
2 B4 2 B4 VDD Power Supply. Bypass VDD to GND with a 1μF capacitor.
3 B3 3 B3 GND Ground C4 4 C4 X- X- Channel Input/Output
5 C3 5 C3 Y- Y- Channel Input/Output
6 C2 6 C2 TIRQ Active-Low Touch Interrupt Output C1 — —- DIN SPI Serial Data Input B1 — — CLK SPI Serial Data Clock Input
9 A1 — — CS SPI Chip-Select Input
10 B2 — — DOUT SPI Data Output
11 A2 11 A2 AUX Auxiliary Input
12 A3 12 A3 Y+ Y+ Channel Input/Output
— — 7 C1 SDA I2C Serial Data Bus Input/Output
— — 8 B1 SCL I2C Serial Data Clock Input
— — 9 A1 A0 I2C Address Input Bit 0
— — 10 B2 A1 I2C Address Input Bit 1 — — — EP Exposed Pad (TQFN only). Connected to ground.
MAX11800–MAX11803
Low-Power, Ultra-Small Resistive Touch-Screen
Controllers with I2C/SPI InterfacePOWER
AND
BIAS
GND
DOUT (A1)
SERIAL INTERFACE
PHYSICAL LAYER
(ANALOG INTERFACE)
SIF
PHY
AUTONOMOUS
MODE ENGINE
LOGIC
CORE
INTERRUPT
GENERATION
ENGINE
SAR
ADC
INTERNAL
CLOCK
TOUCH-
SCREEN
INTERFACE
MUX
VDD
CS (A0)
CLK (SCL)
DIN (SDA)
TIRQV
AUX
MAX11800/MAX11801
FIFO
POWER
AND
BIAS
GND
DOUT (A1)
SERIAL INTERFACE
PHYSICAL LAYER
(ANALOG INTERFACE)
SIF
PHY
LOGIC
CORE
INTERRUPT
GENERATION
ENGINE
SAR
ADC
INTERNAL
CLOCK
TOUCH-
SCREEN
INTERFACE
MUX
VDD
CS (A0)
CLK (SCL)
DIN (SDA)
TIRQV
AUX
MAX11802/MAX11803
Functional Diagrams
MAX11800–MAX11803
Low-Power, Ultra-Small Resistive Touch-Screen
Controllers with I2C/SPI Interface
Detailed DescriptionThe MAX11800–MAX11803 contain standard features
found in a typical resistive touch-screen controller as
well as advanced features found only on Maxim touch-
screen controllers. Standard features included in the
MAX11800–MAX11803 are:4-wire touch-screen interfaceX/Y coordinate measurementTouch pressure measurementDirect conversion operation—requires direct AP
involvementSingle commands—AP initiates all activity, one
command at a timeRatiometric measurement12-bit SAR ADCSingle 1.7V to 3.6V supplyProgrammable touch-detect pullup—50kΩor
100kΩAuto power-down control for low-power operation
Advanced features found in the MAX11800/MAX11801
include:Autonomous conversion operation—minimal AP
involvementOn-chip FIFO—buffers up to 16 consecutive mea-
surementsData tagging—records measurement and touch-
event informationFiltering—reduces noise using straight or median
averagingAperture mode—provides spatial filteringCombined commands—multiple operations per-
formed with a single AP commandUser-programmable acquisition modesProgrammable interrupt output drive
Advanced features found in the MAX11802/MAX11803
include:Data tagging—records measurement and touch
event informationFiltering—reduces noise using straight or median
averagingCombined commands—multiple operations per-
formed with a single AP commandUser-programmable acquisition modesProgrammable interrupt output drive
The MAX11800/MAX11801 operate in one of two top-
level modes: direct conversion mode (DCM) or
autonomous conversion mode (ACM). Direct conver-
sion mode requires the AP to initiate all activity to and
from the MAX11800/MAX11801. DCM is the operating
mode that most standard resistive touch-screen con-
trollers use. ACM allows the MAX11800/MAX11801 to
perform measurements automatically and inform the AP
when they are complete, reducing data transfers on the
serial bus as well as generating fewer interrupt
requests. The MAX11802/MAX11803 operate in DCM
only. DCM requires the AP to initiate all activity to and
from the MAX11802/MAX11803. DCM is the operating
mode that most standard resistive touch-screen con-
trollers use.
Both DCM and ACM support averaging, data tagging,
and combined commands. Certain commands and
operations are only available in DCM, while others are
only available in ACM. See Figures 3a and 3b and
Table 2 for details.
Position MeasurementsPosition measurements determine either the X or Y
coordinates of the point of contact on the panel sensor.
Allow adequate time for the panel to settle when switch-
ing between X and Y measurements. Figure 4 shows
the physical setup of the panel when performing posi-
tion measurements.
The element RTOUCH represents the resistance between
the X and Y planes of the panel sensor. RTOUCH does
not contribute to the error when performing position
measurements. RTOUCH affects the panel settling time
required between each valid measurement.
The panel end-to-end resistance in the direction of
measurement determines the power applied across the
panel. The panel dissipates power in the X elements
when performing an X direction measurement and dis-
sipates power in the Y elements when performing a Y
direction measurement.
MAX11800–MAX11803
Low-Power, Ultra-Small Resistive Touch-Screen
Controllers with I2C/SPI Interface
DIRECT CONVERSION MODECONFIGURATION REGISTER 0x0B BITS[6:5] = 00
PANEL TIMING
0x05
PANEL SETUP
0x69–0x6F
CONFIGURATION
REGISTERS
SETUP, MEASUREMENTS,
AND READBACK COMMANDS
PANEL TIMING (1)
0x05N/A
CONFIGURATION
REGISTERS
SETUP, MEASUREMENTS,
AND READBACK COMMANDS (2)
OPERATION MODE
AUTONOMOUS CONVERSION MODECONFIGURATION REGISTER 0x0B BITS[6:5] = 01, 10, 11
N/A
COMBINED MEASUREMENT
MEASUREMENT: 0x70–0x75
DATA READBACK: 0x52–0x59
COMBINED MEASUREMENT
0x0B
MEASUREMENT: N/A
FIFO READBACK: 0x50
N/A
PANEL MEASUREMENT
MEASUREMENT: 0x78–0x7F
DATA READBACK: 0x52–0x59
AUX
0x0A
AUX MEASUREMENT
MEASUREMENT: 0x76–0x77
DATA READBACK: 0x5A–0x5B
N/AN/A
N/AN/A
MAX11800/MAX11801
OPERATION MODESPANEL SETUP
AVERAGING METHOD
0x03, 0x0BN/AAVERAGING METHOD (1)
0x03, 0x0BN/A
EDGE INTERRUPT MODE
0x01N/AN/AN/A
CONTINUOUS INTERRUPT MODE
0x01N/AN/AN/A
N/AN/A
EVENT TAG (ETAG)
(FIFO NOT USED)DATA READBACK: 0x52–0x59FIFO READBACK: 0x50
FIFO READBACK: 0x50
EVENT TAG (ETAG)
(USES FIFO)
MEASUREMENT TAG (MTAG)
(FIFO NOT USED)DATA READBACK: 0x52–0x59MEASUREMENT TAG (MTAG)
(USES FIFO)
CLEAR-ON-READ
INTERRUPT (1)N/A
AVERAGING
INTERRUPTS
DATA TAGGING
N/AN/AAPERTURE SETTING (1)
0x09, 0x0BN/AAPERTURE
N/AN/A
ADC RESOLUTION AND TIMING
0x02, 0x04, 0x06
ADC RESOLUTION AND TIMING (1)
0x02, 0x04, 0x06N/AN/AADC
PUR AND PUF TIMING
0x07
PUR AND PUF TIMING (1)
0x07N/AN/ATDM TIMING
N/A
NOTE 1: THE CONFIGURATION REGISTERS MUST BE SET UP PRIOR TO ENTERING AUTONOMOUS MODE. THESE REGISTERS CANNOT BE ALTERED WHILE AUTONOMOUS MODE IS ACTIVE.
NOTE 2: COMMANDS RECEIVED WHILE AUTONOMOUS MODE IS ACTIVE ARE IGNORED (EXCEPT READBACK COMMANDS). DURING AUTONOMOUS MODE ALL SCAN ACTIVITIES ARECONTROLLED BY THE MAX11800/MAX11801, BASED ON THE SETTINGS OF THE CONFIGURATION REGISTERS. ALL MEASUREMENT RESULTS ARE STORED IN THE ON-CHIP FIFO.
TINT AND SCANP TIMING (1)
0x08N/AN/AAUTONOMOUS TIMING
MEASUREMENTS
TIRQTIRQ
0x01
TIRQ (1)
0x01
MAX11800–MAX11803
Low-Power, Ultra-Small Resistive Touch-Screen
Controllers with I2C/SPI Interface
DIRECT CONVERSION MODEPANEL TIMING
0x05
PANEL SETUP
0x69–0x6F
CONFIGURATION
REGISTERS
SETUP, MEASUREMENTS,
AND READBACK COMMANDS
OPERATION MODE
N/A
COMBINED MEASUREMENT
MEASUREMENT: 0x70–0x75
DATA READBACK: 0x52–0x59
N/A
PANEL MEASUREMENT
MEASUREMENT: 0x78–0x7F
DATA READBACK: 0x52–0x59
AUX
0x0A
AUX MEASUREMENT
MEASUREMENT: 0x76–0x77
DATA READBACK: 0x5A–0x5B
MAX11802/MAX11803
OPERATION MODESPANEL SETUP
AVERAGING METHOD
0x03, 0x0BN/A
EDGE INTERRUPT MODE
0x01N/A
CONTINUOUS INTERRUPT MODE
0x01N/A
EVENT TAG (ETAG)
(FIFO NOT USED)DATA READBACK: 0x52–0x59
MEASUREMENT TAG (MTAG)
(FIFO NOT USED)DATA READBACK: 0x52–0x59
AVERAGING
INTERRUPTS
DATA TAGGING
N/A
ADC RESOLUTION AND TIMING
0x02, 0x04, 0x06N/AADC
PUR AND PUF TIMING
0x07N/ATDM TIMING
MEASUREMENTS
TIRQTIRQ
0x01
Figure 3b. MAX11802/MAX11803 Operation Modes
MAX11800–MAX11803
Low-Power, Ultra-Small Resistive Touch-Screen
Controllers with I2C/SPI Interface
Pressure MeasurementsZ1 and Z2 measurements determine the resistance
between the two planes within the panel sensor during
a touch (RTOUCH). Depending on the known physical
properties of the panel, one of two equations extract the
value of RTOUCH, providing information about the pres-
sure and area of the touch applied to the panel. Allow
adequate time for the panel to settle when switching
between position and pressure measurements. Figure 5
shows the physical setup of the panel when performing
pressure measurements.
Z1 and Z2 measurements allow observation of the volt-
age on either side of the effective RTOUCHresistance.
With both Z1 and Z2 measurements available, compute
RTOUCHas follows:
If only a Z1 measurement is available, compute
RTOUCHas follows:
The power applied across the panel during pressure
measurements is greatly dependent on RTOUCHand
the physical position of the touch. The maximum power
dissipation in the panel during a pressure measurement
is approximately PZ= VDD2/RTOUCH. This maximumRXTOUCHXPLATEPOSITION
NBITX
NBI=⎛⎜⎞⎟2TTZYPLATEPOSITION
NBITZRY2−⎛⎜⎞⎟−−YY⎜⎞⎟XZTOUCHXPLATEPOSITION
NBITX =⎛⎜⎞⎟−⎛⎜⎞⎟212
OPERATION
MODEPSUPMCCMCTDMLPMAVGFIFOAPERPUR
PUFCONTMTAGETAGX, Y,
Z1, Z2EINTCINTCOR
INT
DCM
MAX11800–
MAX11803 Yes Yes Yes YesNoYesNoNoYesYesYes 2Yes 2YesYes Yes No
ACM
MAX11800/
MAX11801 Yes 1 Yes 1 Yes 1 YesYesYesYesYesYesNoYesYesYesNoNoYes
AUXNo Yes 3 No No—Yes 3NoNoNoNoNoNoNoNoNoNo
Table 2. Operating Modes, Conditions, and Options1In ACM, the choices are limited to X and Y scan, or X and Y and Z1 scan, or X and Y and Z1 and Z2 scan.
2In DCM, MTAG is always used. For DCM with CONT = 0, the following ETAGs are used: 00 = touch present (data valid), 10 = no
touch present (data may be invalid), 11 = measurement in progress (data invalid). For DCM with CONT = 1, the panel cannot be
scanned for a touch because panel setup switches are configured in a measurement mode; therefore, ETAG = 00 is used if a mea-
surement is not in progress, or ETAG = 11 if a measurement is in progress.
3A separate configuration register for delay time, sampling time, averaging, and ADC resolution settings configures the AUX input.
RTOUCHX-
Z1 PRESSURE MEASUREMENT
ADC
INPUT
PANEL
RTOUCH
VDDX-
Z2 PRESSURE MEASUREMENT
ADC
INPUT
PANELVDD
RTOUCH
VDDX-
X POSITION MEASUREMENT
ADC
INPUT
PANEL
RTOUCH
VDDX-
Y POSITION MEASUREMENT
ADCINPUT
PANEL
MAX11800–MAX11803
Low-Power, Ultra-Small Resistive Touch-Screen
Controllers with I2C/SPI Interfacepower dissipation condition is observed when the point
of contact is in the top left corner of the panel sensor.
The planar end-to-end resistance included in the cur-
rent path is minimal at this location. Keep the averaging
and panel settling durations to the minimum required
by the application when pressure measurements are
required. Table 3 summarizes the physical panel set-
tings for supported measurement types.
Touch-Detect Modes and OptionsFigure 6 shows the internal circuitry in the
MAX11800–MAX11803 used to detect the presence of
a touch on the panel. The selection of the pullup resis-
tance value (RTD= touch-detect resistance) and the
durations of the rough pullup interval (PUR = low-
impedance pullup) and fine pullup interval (PUF = high-
impedance pullup) are user-defined.
The MAX11800–MAX11803 revert to the low-power
panel setup when placed in touch-detect mode (TDM).
Figure 6 shows the active panel drive switches (YMSW
and XPSW are omitted for simplicity). TSW is a dedicat-
ed pullup switch used in TDM. TSW is also used during
PUF and TDM. XPSW is activated during PUR periods.
TDRSEL allows the selection of an internal pullup resis-
tor value of either 50kΩor 100kΩ.
The X and Y touch-screen plates create an open circuit
with no current flow in the panel when the panel is not
being touched. In this case, TOUCH (see Figure 6) is
low. When a touch causes contact between the panel X
and Y plates, a current path is created and TOUCH is
pulled high, as long as RPX + RPY(the sum of panel
end-to-end resistance) is much lower than RTD. Typical
open-circuit panel plate resistances range from 200Ω
to 1000Ω.
The MAX11800–MAX11803 enter high-impedance
pullup mode (50kΩor 100kΩ) when the panel is not
being touched. The device is idle in this mode until a
touch is detected. The YMSW and TSW transistors are
on, and the XPSW and PSW transistors are off. With no
touch present, the Y- input of the TSC is at ground and
the X+ input is at VDD - VTN, where VTNis the threshold
voltage of the TSW nMOS device. This is a low-power
mode in which no current is consumed until a panel
touch occurs. When a touch is present on the panel,
the touch-screen controller (TSC) X+ input is pulled low
by the touch panel plate resistance and the YMSW tran-
sistor. This causes TOUCH to assume a logic-high and
the devices either issue the TIRQinterrupt for direct
conversion modes (MAX11800–MAX11803) or begin
self-timed scans for autonomous conversion mode
(MAX11800/MAX11801).
The value of the user-defined RTDdepends on the
characteristics of the panel. To ensure reliable
detection values, worst-case panel resistance must
be checked against RTD. The interaction between
RTDand the panel (or external noise rejecting)
capacitance determines how quickly the panel can
be switched from measurement modes back to
touch monitoring mode without reporting false
touches or erroneous tags due to panel settling.Panel touch status is also required to tag data from a
completed scan and measurement operation. Following
each scan operation, the panel mustbe returned to
TDM to determine if the panel is still being touched and
if the data obtained during the scan operation should
be considered valid. This operation is required since
the panel cannot be monitored for the presence of a
touch during the scan and measurement procedure.
The MAX11800–MAX11803 must return to TDM after
completing a measurement and making a decision on
the touch status of the panel. The measurement proce-
dure is only completed upon resolution of the touch sta-
tus and when data is tagged and available for
readback. The characteristics of the return to TDM and
MODEX+X-Y+Y-REF+REF-XVDDGNDADC_INUX+X-ADC_INUVDDGNDY+Y-ADC_INGNDVDDUY+X-UGNDVDDADC_INY+X-
PURVDD (10Ω)UUGNDU—
TDM or PUFVDD through
50kΩ or 100kΩUUGNDU—
LPMUUUUU—
Table 3. Summary of Physical Panel Settings for Supported Measurement Types
Note:The ADC input is fully differential with the negative input internally connected to GND. The MAX11800–MAX11803 control
access to the PUR, PUF, TDM, and LPM, which do not require setup procedures.indicates unconnected node.
MAX11800–MAX11803
Low-Power, Ultra-Small Resistive Touch-Screen
Controllers with I2C/SPI Interfacethe timing of the decision are configurable through the
touch-detect pullup timing configuration register (0x07).
Program the MAX11800–MAX11803 in the context of
the application to maximize power efficiency and
achieve the desired scan throughput.
PUR and PUFPUR is a fast pullup mode, which uses the main X+
switch in parallel with the resistive pullup to quickly slew
the panel capacitance. PUF uses only the touch-detect
pullup resistor, RTD. PUR and PUF serve the same func-
tion as TDM, but are timed so that the panel can settle
after completing measurements and before rendering
any decisions on the touch status of the panel.
Use the optional PUR mode to reduce the time to tag
data by momentarily placing the panel in a low-imped-
ance (< 10Ω) pullup mode instead of using the avail-
able 50kΩ/100kΩtouch-detection pullup resistors. This
operation forces the monitored TSC input high during
the PUR interval. Once the PUR interval expires, a PUF
interval must be allowed so that the panel can recover
and pull the TSC input low in case a touch is present.
The purpose of the PUR mode is to reduce the time
required to determine touch status by avoiding long
pullup time constants caused by high-capacitance
touch panels and the high-impedance on-chip pullup
resistors (RTD). When a touch is present during PUR
intervals, the current through the low-impedance pullup
(XPSW) and panel combination is significantly higher
than that observed in the PUF mode. The durations in
the PUR mode should be matched to the panel charac-
teristics and the desired scan throughput rates to mini-
mize power dissipation.
While use of the PUR mode is optional, the PUF period
is required for all applications. The PUF interval allows
the panel to resettle following scan or optional PUR
intervals. When a touch is not present, the panel capac-
itance settles toward VDDthrough the internal pullup
switch and a portion of the panel resistance (with the
optional PUR mode disabled). When a touch is present,
the panel capacitance settles toward ground through a
portion of the panel resistance, ideally significantly
lower than the selected pullup impedance, RTD. Allow
enough recovery time for settling through the panel
resistance when using a PUR mode. Figure 7 illustrates
the touch-detection operations.
Idle ModesOnce the PUF period expires, the preceding measure-
ment data is tagged and made available for readback.
The MAX11800–MAX11803 transition to an appropriate
mode depending on the conversion and interrupt mode
selected.
Features Available in the
MAX11800–MAX11803 Averaging ModesThe MAX11800–MAX11803 contain a programmable
averaging filter. When enabled, this feature allows col-
lecting 4, 8, or 16 consecutive samples for each mea-
surement type requested. The number of the samples
for each measurement type is controlled by configura-
tion register 0x03. Averaging can be assigned to each
measurement type. For example, X and Y measure-
ments can use an average of 16 samples, while Z mea-
surements can use one or four samples to save power.
The AUX depth is selected in configuration register
0x0A.
The MAX11800–MAX11803 can be configured to per-
form one of two statistical operations. One option is a
median averaging filter (MAF). The MAF first removes
the lowest and highest values before averaging the
remaining sample set. The second filter type is a
straight averaging filter (SAF), which takes the average
of the entire sample set. Both filter types and
position/pressure averaging are controlled by configu-
ration register 0x0B. Table 4 presents the details of the
median averaging operations of the MAX11800–
MAX11803. For the MAX11800/MAX11801, averaging is
supported in both direct conversion mode and
autonomous conversion mode. The MAX11802/
MAX11803 support only direct conversion mode.
MAX11800–
MAX11803
PUR, PUF, TDM
PUR
VDD
YMSW
XPSW
TDRSELPSW
PANEL
TSW
RTDRTD
PUR, PUF, TDM
(TO MAX11800/
MAX11801 LOGIC)
TOUCH
Figure 6. Touch-Detection Circuitry
MAX11800–MAX11803
Low-Power, Ultra-Small Resistive Touch-Screen
Controllers with I2C/SPI InterfaceTOUCH DETECTPUR MODE
(OPTIONAL)
PUF MODESCAN MODE
MEASUREMENT COMPLETE—
DATA IS KNOWN
POWER ASSISTED PULLUP PERIOD (10Ω) PANEL IS ALLOWED TO RESETTLE BEFORE
DETERMINING DATA VALIDITY
IS THERE A TOUCH
YES = LPM.
NO = TDM.
MEASUREMENT COMPLETE—
DATA IS KNOWN
PANEL IS ALLOWED TO RESETTLE BEFORE DETERMINING DATA VALIDITY
(THROUGH 50kΩ/100kΩ PULLUP)
IS THERE A TOUCH
YES = LPM.
NO = TDM.
DATA VALIDITY IS DETERMINED
(DATA IS TAGGED)
DATA VALIDITY IS DETERMINED
(DATA IS TAGGED)
INITIAL INPUT VOLTAGE
DETERMINED BY LAST SCAN
ACTIVITY
INITIAL INPUT VOLTAGE
DETERMINED BY LAST SCAN
ACTIVITY
FORCED FAST PULLUP USING
10Ω SWITCH
TOUCH NOT PRESENT: TSC INPUT
REMAINS HIGH
TOUCH PRESENT:
TSC INPUT PULLED LOW
TOUCH NOT PRESENT:
TSC INPUT PULLED HIGH THROUGH 50kΩ/100kΩ PULLUP
TOUCH PRESENT:
TSC INPUT PULLED LOW BY PANEL
TIME
TSC INPUT
DIGITAL WAVEFORM
ANALOG WAVEFORM
TIME
DIGITAL WAVEFORM
ANALOG WAVEFORM
NORMAL TOUCH DETECTION (NOTE: NO PUR PERIOD; ALLOW LONG PULLUP TIMES)
FAST PULLUP TOUCH DETECTION (NOTE: INCREASED CURRENT IN PUR MODE DURING TOUCH)
VDD
TSC INPUT
VDD
TOUCH DETECTPUF MODESCAN MODE
MAX11800–MAX11803
Low-Power, Ultra-Small Resistive Touch-Screen
Controllers with I2C/SPI Interface
Combined CommandsCombined commands reduce AP interaction with the
MAX11800–MAX11803 by allowing multiple measure-
ments. For example, the MAX11800–MAX11803 can be
instructed to provide X and Y data, or X and Y and Z1
data, or X and Y and Z1 and Z2 data using a single
command.
Data TaggingIn direct conversion modes, all measurement data is
contained in a 16-bit word. X, Y, Z1, and Z2 information
is stored independently. Each word consists of 12 bits
of measurement data plus a 2-bit measurement type
(MTAG) and a 2-bit event tag (ETAG). The measure-
ment tag identifies whether the data represents an X, Y,
Z1, or Z2 result. The event tag indicates the point at
which the data is sampled (initial, midpress, or release)
during the touch event. When trying to read a result that
is pending, the entire data stream is read back as
FFFFh and the event tag as 11b, indicating that the cor-
responding measurement is in progress and that the
data stream is to be ignored. For combined commands,
all data locations requested by the command are
marked FFFFh, pending the completion of the entire
command and the proper tagging of the data. See
Table 5.
Direct conversion modes do not use the internal FIFO
or support the aperture function (see the Aperture
Modes and Optionssection). Each measurement type
uses a single location in the (16-bit) memory. The AP
must retrieve the data from the last requested measure-
ment before moving on to the next measurement of the
type.
Auxiliary measurement data is not tagged because it is
not related to panel operation. Auxiliary measurement
data is stored and read back identically to the other
direct conversion data. The tag locations for auxiliary
measurement data are always set to 0000b, unless the
read occurs when an auxiliary measurement is in
progress. In this situation, the tag locations read 1111b
and the data stream reads back FFFFh.
Low-Power ModesThere are also two low-power modes, LPM and TDM.
LPM only applies when in DCM with edge interrupt
mode or ACM during periods following a conversion
where the panel was observed to be touched and a
subsequent panel measurement is required and/or
scheduled.
During LPM, all circuitryis off, including the on-chip
touch-detect pullup resistors used in the touch-detect
circuitry. In direct conversion modes, a user-request ini-
tiates the next operation and all circuitry is off until a
user-command is received. Therefore, the current con-
sumption is primarily due to junction leakage. In
autonomous conversion mode, an on-chip oscillator
and timer are constantly running. Therefore, the device
current consumption is primarily determined by the
oscillator and timer.
During TDM, all circuitry is off except the on-chip pullup
resistor. This is an untimed mode (oscillator and timer
are off) for both ACM and DCM (no digital current). This
mode only consumes current through the on-chip
pullup resistor when a touch is present. The device can
be powered down through register 0x0B when no panel
input is expected or needed, and, therefore, no power
is consumed through the panel.
INDEX1514131211109876543210Byte MSB Byte LSB Byte
12-Bit Content Position MSBs Position LSBs Measure Event
8-Bit Content Position Data Trailing Zeros* Measure Event
Table 5. Data Word Structure (All Direct Conversion Modes)
AVERAGING MODENUMBER OF
SAMPLES TAKEN
NUMBER OF HIGH
SAMPLES REMOVED
NUMBER OF LOW
SAMPLES REMOVED
NUMBER OF
REMAINING SAMPLES
AVERAGED112224
Table 4. Median Averaging Operations
*When using averaging with 8-bit conversions, these positions may be filled with fractional data due to averaging operations.
MAX11800–MAX11803
Low-Power, Ultra-Small Resistive Touch-Screen
Controllers with I2C/SPI Interface
Features Available in the
MAX11800/MAX11801 Only
Autonomous ModeThe MAX11800/MAX11801 can perform measurements
automatically without the AP involvement, and is
referred to as autonomous conversion mode (ACM).
When operating in ACM, the MAX11800/MAX11801 use
an on-chip FIFO to store measurement results. As each
new data is written to the FIFO, an interrupt is generat-
ed. The AP can choose to service (read) the FIFO result
after each interrupt or wait until the FIFO is full then
read the entire FIFO contents at once. The AP can also
read the contents of the FIFO at any time. See the
Autonomous Conversion Modesection for a further
description of operations.
ApertureThe MAX11800/MAX11801 contain a feature referred to
as aperture. It is only available on the MAX11800/
MAX11801 when operating in autonomous conversion
mode. The aperture feature creates an invisible rectan-
gle around a touch location within the MAX11800/
MAX11801 hardware. The size of the rectangle is user
programmable. One application of the aperture feature
is to provide “spatial hysteresis.” Spatial hysteresis can
be useful for applications that require lower resolution
touch accuracy without requiring the AP to handle the
mathematics involved to filter out extraneous data.
Another application would be to use the aperture fea-
ture to implement simple single finger or stylus ges-
tures. See the Using Aperture Mode section for a
further description of operations.
Panel Setup, Measurement, and Scan CommandsTo simplify measurement procedures, the MAX11800–
MAX11803 support three types of commands: panel
setup commands (PSU), panel measurement commands
(PMC), and combined measurement commands (CMC).
In direct conversion mode, the MAX11800/MAX11801
can use all three types of commands. Using individual
panel setup and measurement commands allow for a
high degree of customization based on decisions made
by the AP, while using combined commands signifi-
cantly simplifies the complete measurement process
and reduces communications between the AP and the
MAX11800–MAX11803.
In autonomous mode, the MAX11800/MAX11801 use
combined commands to control and automate all
aspects of panel setup, measurements, and timing. See
the Operating Mode Configuration Register (0x0B)sec-
tion for more details.
Direct Conversion Mode OperationsIn direct conversion mode, the AP requests individual
panel setup and conversion operations or automated
combinations of measurements (X and Y, X and Y and
Z1, or X and Y and Z1 and Z2 combined). Unlike
autonomous conversion modes, the AP maintains control
over the initiation of panel setup, measurements events,
and the sampling frequency. Figure 8 shows the state
machine transitions for direct conversion mode.
Interrupt ModesThe MAX11800–MAX11803 support two direct conver-
sion interrupt modes. The two direct conversion modes
are the continuous interrupt mode (CINT) and the edge
interrupt mode (EINT).
Continuous Interrupt ModeIn continuous interrupt mode, the panel returns to TDM
and idle. The current status of the panel is then sent
through TIRQ. The continuous interrupt mode is the
least efficient mode in current consumption for long
duration of touches. The power consumption is approxi-
mated by PTOUCH = VDD2/RPU. The power consump-
tion levels observed when the panel is not touched is
limited by the junction leakage currents of the
MAX11800–MAX11803.
Procedure:The MAX11800–MAX11803 idle in TDM.
The TIRQoutput goes low when a touch is detected on
the panel indicating to the AP that a touch is present
and a measurement operation starts.
The AP requests specific panel measurements through
the serial interface. TIRQstays low during panel setup
and measurement operations. Once a measurement is
complete (with the “continuous” bit, CONT = 0, see
Table 1), the MAX11800–MAX11803 check for the con-
tinued presence of a touch on the panel and tag the data
accordingly (see Table 6). The duration of this operation
is programmable, specified in the touch-detect pullup
timing configuration register (0x07). After the data is
tagged, the data is available for readback through the
serial interface. The MAX11800–MAX11803 return to
TDM and return control of TIRQto the TDM circuitry.
TIRQstays low while a touch remains present, indicating
further measurements are required, otherwise TIRQgoes
high until a new touch is observed.
Continuous interrupt mode (CINT) allows the complete
control over the measurement operations and direct obser-
vation of the touch status of the panel. Figure 9 shows the
polling of TIRQwhen other functions share the TIRQbus. In
the illustration of Figure 9, no ‘10’ event tag is observed
because the release occurs during a TDM period.
Edge Interrupt ModeWhen a touch is present on the panel in edge interrupt
mode, the MAX11800–MAX11803 return to an untimed
high-impedance mode once data tagging operations are
complete. In edge interrupt mode, the duration of a touch
is determined by the tags applied to the measurement
data. Data tagged as initial (00) or midpress (01) indicates
the user needs to continue to scan the panel until a
release is observed. In this state, there is no need to con-
tinue monitoring the touch status prior to the next request-
ed measurement. If a panel touch is not present, data is
tagged as release (10) and the MAX11800–MAX11803
idle in TDM continuously, issuing an interrupt only when
the next panel touch is initiated.
The operation described in the preceding paragraph
makes the edge interrupt mode more power-efficient
than the continuous interrupt mode. However, the edge
interrupt mode requires continuous scanning of the
panel until a release (10) event is observed. Otherwise,
the MAX11800–MAX11803 do not idle in TDM and are
not able to recognize a change in touch status. New
touches are not recognized and new interrupts are not
issued if a release event is not detected before stop-
ping the conversion sequence.
MAX11800–MAX11803
Low-Power, Ultra-Small Resistive Touch-Screen
Controllers with I2C/SPI InterfaceACQUIRE
ACQUIRE
TOUCH
DETECT
TOUCH-
DETECT
FINE
PULLUP
TOUCH-
DETECT
FINE
PULLUP
TIME IS UP
SETUP
PANEL
ACQUIRE
DETECT
AUX
ACQUIRE
AVERAGECONVERSIONLASTCONVERSION
NOT LAST OR
CONTINUOUS
LAST AND NOTCONTINUOUSNOT LAST OR
CONTINUOUS
LAST AND NOTCONTINUOUS
TIME IS UP
DONE AND
CONTINUOUS
DONE AND
CONTINUOUS
AVERAGE
CONVERSION
LAST
CONVERSION
COMMAND
COMMAND
COMMAND
USER COMMAND
INTERNAL TRANSITION
SETUP
PANEL
SETUP
PANEL
Figure 8. State Machine Transitions (Direct Conversion Mode)—MAX11800–MAX11803
MEASUREMENTMTAG[3:2]X 00
Y 01
Z1 10
Z2 11
EVENTETAG[1:0]Touch (data valid) 00
N/A (not used) 01
No touch present (data invalid) 10
Measurement in progress (data invalid) 11
Table 6. Measurement and Event Tags
(Continuous Interrupt Mode)
MAX11800–MAX11803
Low-Power, Ultra-Small Resistive Touch-Screen
Controllers with I2C/SPI Interface
Procedure:The EINT mode reduces TIRQactivity.
During EINT, the MAX11800–MAX11803 idle in a TDM.
TIRQgoes low when a new touch is detected on the
panel. TIRQstays low for a fixed duration as specified
in the configuration register 0x01, indicating to the AP
that a touch is present and measurements are required.
The AP requests specific panel setups and measure-
ments through the serial interface using panel setup
and conversion commands after TIRQgoes low. Once
a measurement is complete (with CONT = 0), the
MAX11800–MAX11803 check for the continued pres-
ence of a touch and tag the data accordingly. See
Table 7. The duration of this operation is programma-
ble, specified in the Touch-Detect Pullup Timing
Configuration Register (0x07) section. After the data is
tagged, it is available for readback through the serial
interface. The MAX11800–MAX11803 do not return to
TDM when the panel touch is still present (ETAG = 00,
01), but remain in an LPM awaiting further measure-
ment commands. The devices return to TDM when the
panel touch is no longer present (ETAG = 10) and
return control of the TIRQinterrupt to the TDM circuitry
to await the next touch event.
After a touch is indicated, the AP must continue to issue
conversion commands until the touch is removed, alert-
ing the AP when the panel is released (by ETAG = 10).
The MAX11800–MAX11803 return to TDM and observe
the start of the next touch event. Panel commands
issued with CONT = 1 are not capable of fulfilling this
requirement.
The EINT mode provides the least interrupt activity and
the lowest power consumption. Use EINT mode for
general touch-screen applications and applications
requiring high resolution in space and time. When the
TIRQbus is shared with other functions, poll the gener-
al status register (0x00) to detect the presence of an
interrupt. See Figure 10.
MEASUREMENTMTAG[3:2]X00
Y011011
EVENTETAG[1:0]Initial touch (data valid)00
Midpress (data valid)01
Release/no touch present
(data invalid)10
Measurement in progress
(data invalid)11
Table 7. Measurement and Event Tags
(Edge Interrupt Mode)DCM SCAN
ETAG = 00
DCM SCAN
ETAG = 00
DCM SCAN
ETAG = 00
TDMTDMTDMTDM
TIRQ
PANEL
TOUCH
BEGINNING OF TOUCH EVENTEND OF TOUCH EVENT
tAPtSD
READBACK OPERATIONS ARE NOT SHOWN, BUT ARE EXECUTED DURING TDM PERIODS.
SCAN INTERVAL (tAP) IS CONTROLLED BY THE AP AND THE INITIATION OF DM SCAN EVENTS.
SCAN DURATION (tSD) IS A FUNCTION OF THE SCAN TYPE AND CONFIGURATION SETTINGS.
DCM = DIRECT CONVERSION MODE
INITIATED AND CONTROLLED BY
THE AP
Figure 9. Continuous Interrupt Mode (Direct Conversion Mode)
MAX11800–MAX11803
Low-Power, Ultra-Small Resistive Touch-Screen
Controllers with I2C/SPI Interface
Panel Setup Commands Panel setup commands configure the touch panel prior to
a measurement. Panel setup commands allow the panel
to fully settle before performing a measurement. The
panel setup command summary is shown in Table 8. See
the register map in the Status and Configuration Registers
section for details on the panel setup timing options for X,
Y, Z1, and Z2 measurements.
The continuation bit (CONT) of the panel setup com-
mand programs the MAX11800–MAX11803 to maintain
the present panel setting at the end of the command
(CONT = 1). Panel setup commands assume a logical
progression to an appropriate measurement. For exam-
ple, when the MAX11800–MAX11803 are in the X panel
setup mode, the devices can proceed to an X measure-
ment mode only. The devices return to LPM when an
incompatible command follows a panel setup com-
mand. See Figure 11. For most applications adequate
time for panel setup is available as an integral part of
the panel measurement commands; configured using
the panel setup timing configuration register, 0x05. The
dedicated panel setup commands are primarily provid-
ed to support applications where the AP needs to con-
trol panel setup directly or long panel setup time is
required.
Panel Measurement CommandsA measurement command selects one of the four phys-
ical setup options: X, Y, Z1, or Z2.
All panel measurement commands include timed inter-
vals to power up both the internal ADC and the panel
with programmable durations. The delayed conversion
time (tD_CV, delayed conversion configuration register
(0x06)) governs the time that the panel and the ADC
need to settle prior to the initiations of conversions. The
minimum delayed conversion time is 10μs, which is the
time the internal ADC needs to power up. If more set-
tling time is required, increase the panel settling time
HEXACCESSPAIRABLECOMMAND LENGTHOPERATION0x69h Write No 8 X = panel setup
0x6Bh Write No 8 Y = panel setup
0x6Dh Write No 8 Z1 = panel setup
0x6Fh Write No 8 Z2 = panel setup
Table 8. Panel Setup Command SummaryDCM SCAN
ETAG = 10
DCM SCAN
ETAG = 01
DCM SCAN
ETAG = 00
TDMLPMLPMTDM
TIRQ
PANEL
TOUCH
BEGINNING OF TOUCH EVENTEND OF TOUCH EVENT
tAPtSD
READBACK OPERATIONS ARE NOT SHOWN, BUT ARE EXECUTED DURING TDM PERIODS.
TIRQ DURATION (tIRQ) IS SPECIFIED BY THE GENERAL CONFIGURATION REGISTER (0x01).
SCAN INTERVAL (tAP) IS CONTROLLED BY THE AP AND THE INITIATION OF DM SCAN EVENTS.
SCAN DURATION (tSD) IS A FUNCTION OF THE SCAN TYPE AND CONFIGURATION SETTINGS.
tIRQINITIATED AND CONTROLLED BY
THE AP
DCM = DIRECT CONVERSION MODE
Figure 10. Edge Interrupt Mode (Direct Conversion Mode)—MAX11800–MAX11803
MAX11800–MAX11803
Low-Power, Ultra-Small Resistive Touch-Screen
Controllers with I2C/SPI Interfaceby delaying the conversion time or by adding an addi-
tional panel setup time (tPSU) using the panel setup tim-
ing configuration register (0x05). The advantage of
using a dedicated panel setup time is that the ADC
does not consume power during this interval. The
required panel setup time is a function of the panel
end-to-end resistance, the capacitance of the panel,
and any board-level components.
When using a measurement command with CONT = 1 in
a direct conversion mode, the devices remain in the
requested setup mode in preparation for the succeeding
measurement. The panel does not return to TDM/LPM
and the interrupt status is not modified as a result of a
measurement command with CONT = 1 issued. See
Figure 12.
Combined Commands In direct conversion modes, the panel returns to a TDM
at the conclusion of a combined command and all data
are tagged accordingly. The MAX11800–
MAX11803then idle in a low-power mode determined
by the interrupt mode selected. See Figure 13.
Auxiliary Measurement CommandThe MAX11800–MAX11803 support measurement of an
auxiliary input using the internal ADC in direct conver-
sion mode only. When programmed, the devices sam-
ple and quantize the voltage at AUX using VDDas the
ADC reference. The MAX11800–MAX11803 store the
result in the same manner as X, Y, Z1, and Z2 measure-
ments, but do not add data tagging. The devices also
support averaging functions. Auxiliary measurements
do not require any panel setup procedure. There is no
HEXACCESSPAIRABLECOMMAND LENGTHFUNCTION0x70h Write No 8 X, Y = combined command measurement
0x72h Write No 8 X, Y, Z1 = combined command measurement
0x74h Write No 8 X, Y, Z1, Z2 = combined command measurement
0x76h Write No 8 AUX = conversion
0x78h Write No 8 X = measurement, CONT = 0
0x79h Write No 8 X = measurement, CONT = 1
0x7Ah Write No 8 Y = measurement, CONT = 0
0x7Bh Write No 8 Y = measurement, CONT = 1
0x7Ch Write No 8 Z1 = measurement, CONT = 0
0x7Dh Write No 8 Z1 = measurement, CONT = 1
0x7Eh Write No 8 Z2 = measurement, CONT = 0
0x7Fh Write No 8 Z2 = measurement, CONT = 1
Table 9. Panel Measurement Command SummaryLPM
X PSU CMD
X MEAS CMDN
Y PSU CMD
Y MEAS CMD
Z1 PSU CMD
Z1 MEAS CMD
Z2 PSU CMD
Z2 MEAS CMD
MAX11800–MAX11803
Low-Power, Ultra-Small Resistive Touch-Screen
Controllers with I2C/SPI InterfacePANEL SETUP (PSU) FOR X, Y, OR Z DRIVESETTING IS MAINTAINED UNTIL NEXT COMMAND (CONT = 1).
PANEL SETUP COMMANDS (DIRECT CONVERSION ONLY)
MEASUREMENT COMMANDS (DIRECT CONVERSION ONLY)
SINGLE CONVERSION WITH CONT = 1
SINGLE CONVERSION WITH CONT = 0
AVERAGED CONVERSION WITH CONT = 0
SETUP
(tPSU + tD_CV)
ADC
ACQUISITION
ADC
CONVERSION
ADC
ACQUISITIONi
ADC
CONVERSIONi
PSUDATA IS LOGGED.
SETTING IS MAINTAINED UNTIL NEXT COMMAND (CONT = 1).
AVERAGED CONVERSION WITH CONT = 1
SETUP
(tPSU + tD_CV)PSU
AVERAGED DATA IS LOGGED.
SETTING IS MAINTAINED UNTIL NEXT COMMAND (CONT = 1).
DATA IS TAGGED AND LOGGED.
THE MAX11800–MAX11803 RETURN TO LPM OR TDM, ACCORDING TO IRQ MODE.
AVERAGED DATA IS TAGGED AND LOGGED.
THE MAX11800–MAX11803 RETURN TO LPM OR TDM, ACCORDING TO IRQ MODE.
NAVG
NAVG
SETUPADC
ACQ
ADC
CONV
PUR
(OPTIONAL)
ADC
ACQi
ADC
CONVi
PUR
(OPTIONAL)
PUF
SETUPPUF
Figure 12. Panel Setup and Measurement Commands—MAX11800–MAX11803
combined command which includes an auxiliary mea-
surement. Register 0x0A specifies the configuration for
auxiliary measurements.
In CINT, the MAX11800–MAX11803 continue to monitor
for the touch status of the panel. The devices report any
change in touch status in real time during an auxiliary
measurement procedure.
When performing auxiliary measurements in edge
interrupt mode, the MAX11800–MAX11803 temporarily
suspend the panel touch monitoring. The devices noti-
fy the AP after the completion of the auxiliary measure-
ment when a new touch occurs during the auxiliary
measurement.
MAX11800–MAX11803
Low-Power, Ultra-Small Resistive Touch-Screen
Controllers with I2C/SPI InterfaceX AND Y COMMANDS
SINGLE CONVERSIONSDATA EVENT TAGGING
AVERAGED CONVERSIONS
PSU
ACQ
CONV
PSU
ACQ
CONV
PUR
(OPTIONAL)PUF
PSU
ACQ
CONV
PSU
ACQ
CONV
PUR
(OPTIONAL)PUF
X, Y, AND Z1 COMMANDS
NAVGXNAVGY
SINGLE CONVERSIONS
AVERAGED CONVERSIONS
PSU
ACQ
CONV
PSU
ACQ
CONV
PUR
(OPTIONAL)PUF
PSU
ACQ
CONV
PSU
ACQ
CONV
PSU
ACQ
CONV
PSU
ACQ
CONV
PUR
(OPTIONAL)PUF
NAVGZ1
X, Y, Z1, AND Z2 COMMANDS
SINGLE CONVERSIONS
AVERAGED CONVERSIONS
PSU
ACQ
CONV
PSU
ACQ
CONV
PUR
(OPTIONAL)PUF
PSU
ACQ
CONV
PSU
ACQ
CONV
PSU
ACQ
CONV
PSU
ACQ
CONV
CONV
ACQ
ACQ
CONV
PUR
(OPTIONAL)PUF
NAVGZ2
NAVGXNAVGY
NAVGZ1NAVGXNAVGY
Figure 13. Combined Commands—MAX11800–MAX11803